Resources & Support
Support for advanced manufacturing
Technical Papers
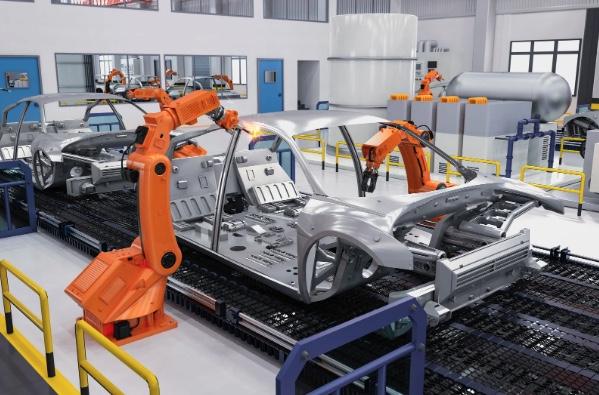
Five causes of robot drift (and how to eliminate them)
Robot drift, where advanced manufacturers experience small inaccuracies in robot cell performance over time, can lead to quality issues, compliance failures, costly downtime and wasted materials. Production efficiency can be seriously impaired, and extremely costly.
In this article, we identify five causes, and how to avoid the unwelcome consequences of robot drift.
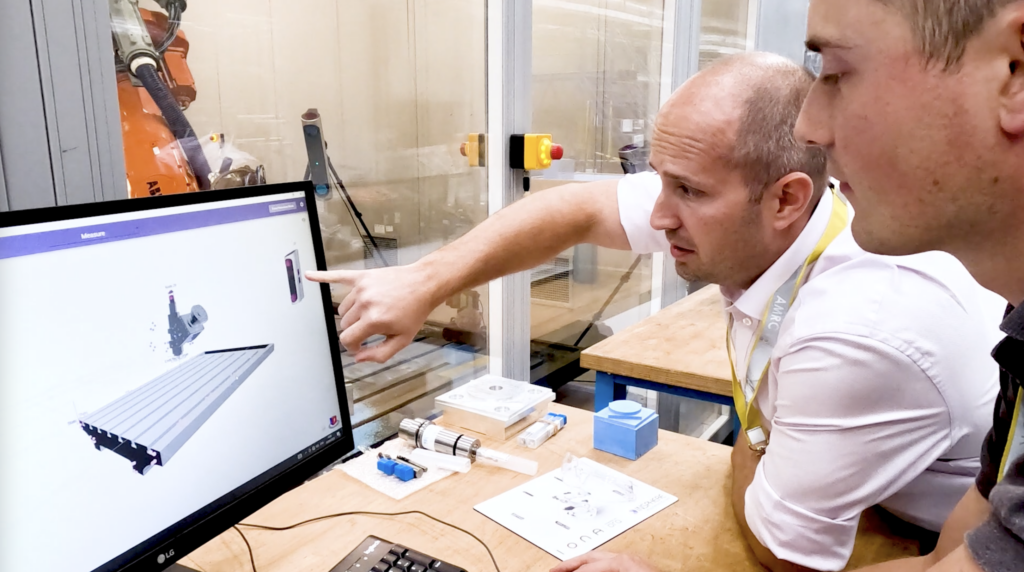
In-process metrology brings great benefits to advanced manufacturing - why is it not more widely accepted in UK operations?
This whitepaper summarises a round-table discussion between senior engineers working for leading UK aerospace and automotive organisations, as well as senior engineers from UK research centres.
It provides a comprehensive overview of the objectives, challenges and considerations of those working directly with robots and automation. It highlights the need for increased education of metrology and photogrammetry solutions across sectors, to propel the industry forward to better align with the aspirations of Industry 4.0.
The round-table discussion was part of project ACCUFAS, a project focused on developing IONA technology to facilitate high accuracy robot control within the aerospace sector, chaired by Insphere’s Operations Manager at the AMRC Factory 2050 in November 2023.
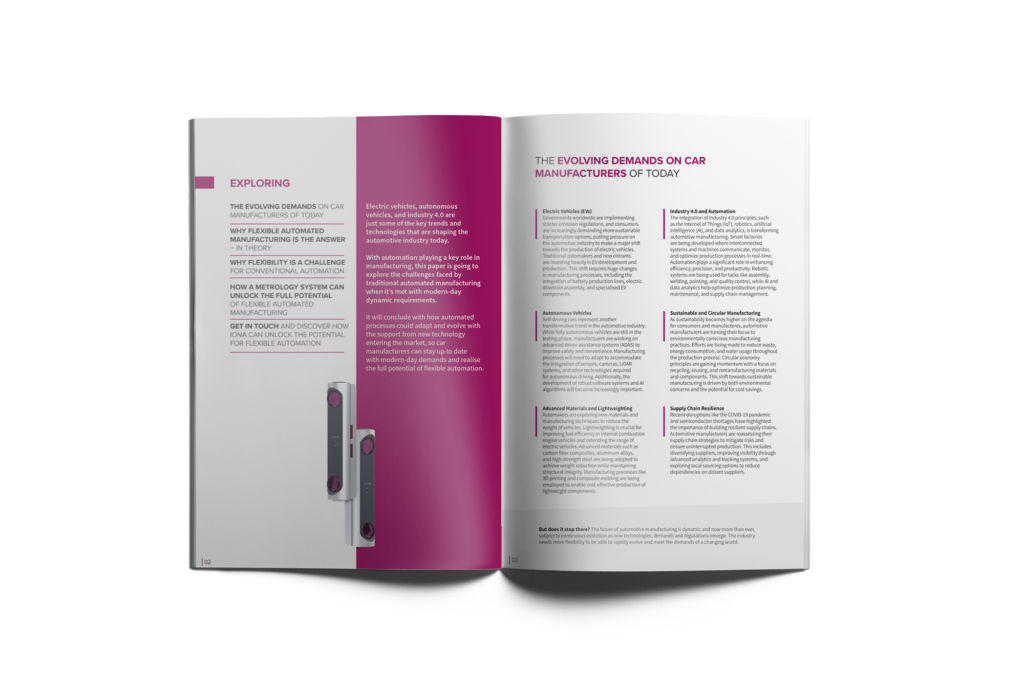
Automation and the challenges facing car makers, is a flexible manufacturing system the answer?
Get insight into the evolving demands on car manufacturers, why (in theory) flexible manufacturing is the answer and the realities of why flexibility is a challenge for conventional automation.
With automation playing a key role in manufacturing, this paper explores the challenges faced by traditional automated manufacturing when met with modern-day dynamic requirements.
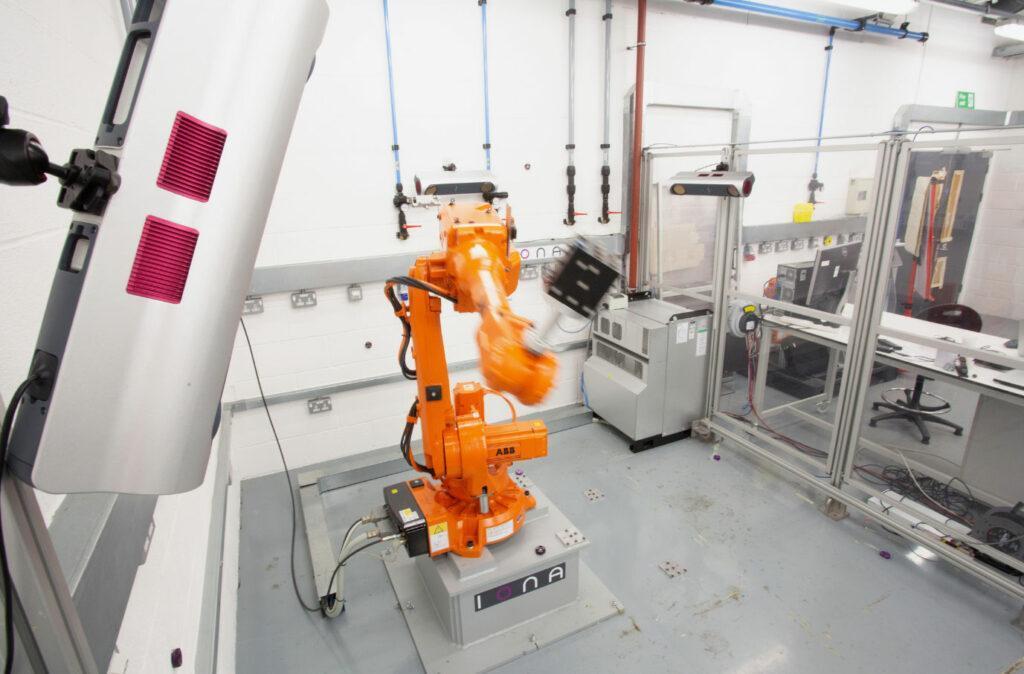
3 Steps to improving Robot Accuracy by measuring, teaching and monitoring process performance
This article also tackles a range of assumptions associated with robots: repeatability vs accuracy, the interplay between robot payload and stiffness, as well as flexibility vs in-process adaptability.
A Data-Driven Approach to Improving Robot Performance, Productivity & Efficiency
Lorem ipsum dolor sit amet, consetetur sadipscing elitr, sed diam nonumy eirmod tempor invidunt ut labore et dolore magna aliquyam erat, sed diam voluptua. At vero eos et accusam et justo duo dolores et ea rebum. Stet clita kasd gubergren, no sea takimata sanctus est Lorem ipsum dolor sit amet.
Passionate about robotics and automation?
Stay up to date with the latest industry news, IONA product development, software upgrades, technical papers and much more
FAQ's
IONA is a network of sensors designed to monitor and control industrial robots. The system can monitor the movement of the robot but also the relationship between the robot and the fixture or work object that it’s performing a task on.
IONA is built on the principle of a network of sensors (nodes) permanently and discreetly deployed in a manufacturing environment. By observing motion from multiple vantage points, accuracy is increased and line-of-sight issues are removed. The expansible system scales to your needs and works at a cell to a factory level.
The System is formed part of:
Nodes: Each node tracks the 6DOF motion of targets in 3D within its field of view. It is robustly designed and is connected via a single data and power POE cable. Nodes can be mounted on pre-existing guarding and are able to account for environmental instability.
Tile: Each tile is comprised of a pattern of retro-reflective spheres. These tiles are located sparsely around the cell to provide a reference frame. They are also used to track additional points of interest such as: parts, fixtures and tooling.
TCP Targeting: Discrete Targeting on the robot end-effector to permanently monitors the position and the relationship with the work object.
Controller: The controller manages the network of nodes, combining the 6DOF locations each node returns and calculates an accurate result using the proprietary IONA algorithms. Data output is
The system consists of a series of nodes. These are simply mounted on automation cell guarding around the periphery of a robot cell. And they’re able to capture data from lots of different line of sight meaning that you can continually monitor a process as that process is running. The nodes themselves don’t need stable mounting. They can resect their own position in space so they can be mounted simply on the cell guarding itself. To connect the series of nodes. It’s a simple Power over Ethernet cable. So one cable that provides the data interface but also the powering to the node. This makes installation and setup of the system very simple and can be done in a short space of time.
The sensors themselves measure small retro reflective spherical targets. These are passive targets and don’t need any cabling to connect them. These targets can be placed at strategic points on the robots or on the fixture that the robot is working on, or even to represent the cell datum structure. From the targets we’re able to construct 3D coordinate frames. Within our software then we can track how these frames move and also the relationship between the various frames that we’re monitoring.
The IONA system consists of both hardware and software. The hardware is the series of nodes, the controller, the targeting everything that’s required to capture the data.
The IONA system also consists of our software, our ORA platform. ORA is used to collect the data and also perform analysis before feeding that data back into the system
The IONA system is robot agnostic. We can work with any robot, be that a KUKA, or ABB, a FANUC. The things that change may be how we interact and pass data to the robot controller.
The data from IONA can be used at three key stages of manufacturing.
- It can be used at the commissioning stage to correct for the differences that occur between the simulation or the offline programme and the physical setup of the cell. This data can also be used to feed back into the digital environment to update the digital twin, meaning that there is an exact replica in the digital world as operating in the physical world.
- The second stage that we can use this data at is as a process enabler to increase the accuracy of an automated process.
- We can do this in a number of ways. We can achieve a better alignment between the work object and the robot itself but we can also use our data to perform a calibration in situ on the robot. This calibration can be run as a one off when a cell is first set up, or it can be run each time a process operates.
- We can also use our data as part of a live feedback loop. So the process is continuously correcting and iterating based on the alignment or repositioning of elements within the cell.This can improve the dynamic accuracy of any given process.
- The third stage, when we can use our data is as part of a process control approach. By continually monitoring a process over time we can start to spot the trends in the data and understand whether our
Customer Portal - Coming Soon
Discover the user guide, the most recent software updates, raise a ticket or send a message to our technical team.