The importance of properly calibrated robots in high-value manufacturing
Background
In the realm of high-value manufacturing, precision and reliability are essential. This is especially true in industries such as automotive, aerospace, and nuclear, where the stakes are extraordinarily high. Central to maintaining this precision and reliability is the correct and regular calibration of robots.
The Importance of Calibration
- Precision and Accuracy
In high-value manufacturing, even the smallest deviation can lead to significant issues. Robots that are not properly calibrated can produce components that do not meet stringent specifications.
In the automotive industry, for example, this can lead to misaligned parts, affecting the performance and safety of vehicles.
In aerospace, where tolerances may be even tighter, an uncalibrated robot could result in components that fail to meet critical aerodynamic or structural requirements, potentially jeopardising safety.
In the nuclear sector, precision is paramount to ensure the integrity of reactor components and overall plant safety.
Proper calibration ensures that robots perform their tasks with the highest degree of accuracy, reducing the risk of defects.
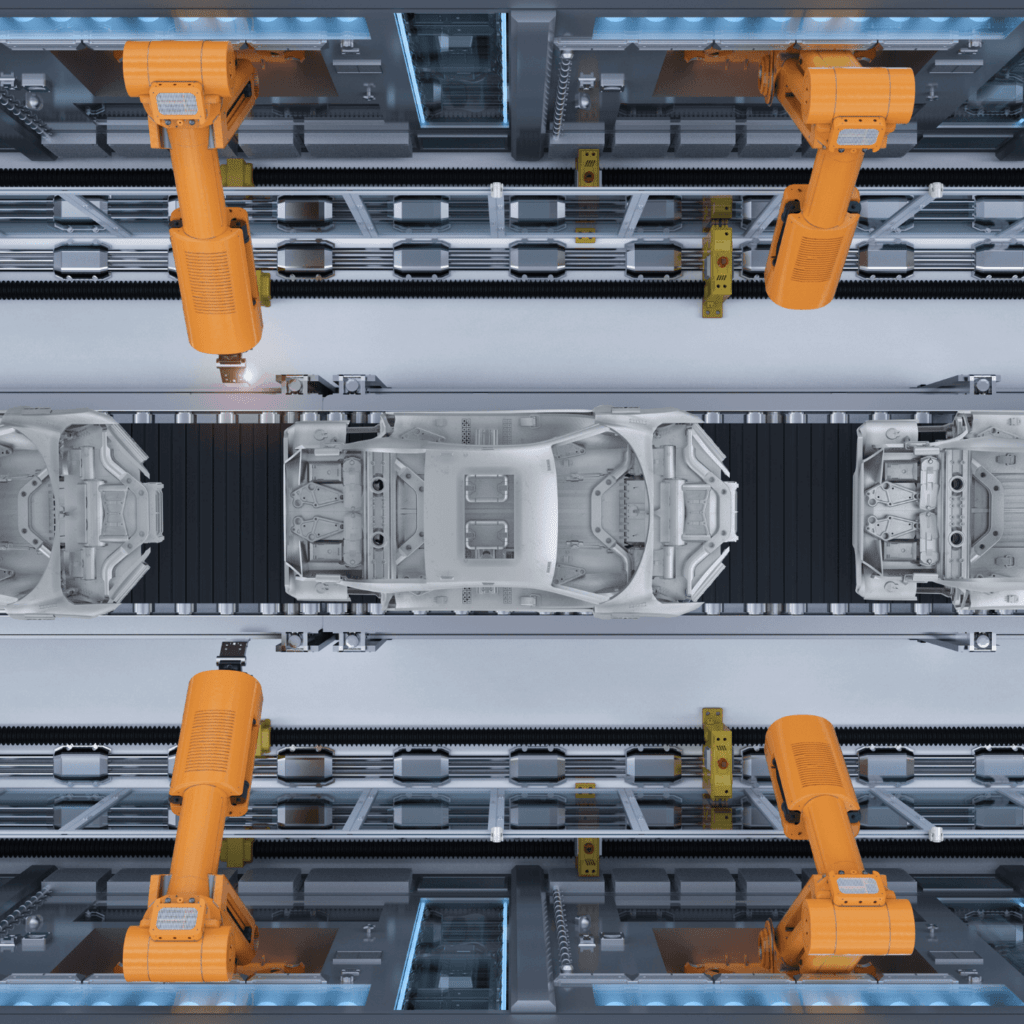
- Consistency and Reliability
Regular calibration of robots ensures consistent performance over time, crucial for maintaining product quality and operational efficiency.
A correctly calibrated robot in the automotive industry will consistently produce parts that fit together perfectly, facilitating smooth assembly processes and reducing downtime. In aerospace, consistency in component production ensures that every aircraft meets the same high standards. In the nuclear industry, reliability is critical for maintaining safety and avoiding costly shutdowns or repairs.
Properly calibrated robots deliver reliable performance, which is essential for maintaining high standards and meeting production schedules.
The Benefits of Proper Calibration
- Enhanced Product Quality
One of the primary benefits of regular robot calibration is the improvement in product quality.
High-precision manufacturing relies on robots that can consistently produce parts within exacting tolerances. In the automotive industry, this leads to vehicles with better performance and fewer defects. In aerospace, it ensures the safety and efficiency of aircraft. In the nuclear sector, it means reactor components that meet strict safety and performance criteria.
Enhanced product quality leads to greater customer satisfaction and a stronger reputation for manufacturers.
- Cost Savings
Proper calibration can lead to significant cost savings by reducing waste and minimising the need for rework. In high-value manufacturing, materials and components can be extremely expensive. By ensuring that robots are precisely calibrated, manufacturers can avoid producing defective parts that must be scrapped or reworked.
This not only saves material costs but also reduces labour costs associated with rework and improves efficiency.
- Increased Operational Efficiency
Calibrated robots operate more efficiently, reducing cycle times and increasing throughput.
In the automotive industry, this means faster production lines and the ability to meet market demands more effectively. In aerospace, it translates to the timely production of aircraft components, ensuring that delivery schedules are met. In the nuclear sector, it means more efficient and safe production processes, reducing the risk of costly delays.
The Risks of Neglecting Calibration
Neglecting robot calibration can lead to a host of problems, including production delays, increased costs and safety risks.
Uncalibrated robots can produce defective parts, leading to production slowdowns as issues are identified and corrected.
This also leads to increased waste and the need for rework, driving up production costs.
In the aerospace and nuclear industries, incorrect calibration can compromise safety, potentially leading to catastrophic failures.
Conclusion: The need for expert calibration
Given the critical importance of robot calibration, it is essential to employ experts in this field. Calibration experts have the knowledge and experience to ensure that robots are operating at peak precision, using specialist tools and techniques to fine-tune robotic systems, ensuring optimal performance.
Proper and regular calibration of robots is vital in high-value manufacturing sectors. The benefits of enhanced product quality, cost savings, and increased operational efficiency far outweigh the risks of neglecting calibration.
By using experts to ensure precise calibration, manufacturers can maintain the highest standards of quality and safety, securing their position in a competitive market.