Digital Twin
Unlocking the true potential of industrial robots.
Introduction to Digital Twin
The concept of the digital twin is to replicate the manufacturing process in the virtual world, accurately simulating the factory environment and processes operating within it. This allows engineers to plan changes to the production configuration, implement new processes or introduce new products in the virtual world before sending the changes to the shopfloor.
This allows changes to be assessed, programmed and validated offline before needing to change the physical system. This can be invaluable in enabling flexible manufacturing solutions and critical in reducing time to bring.
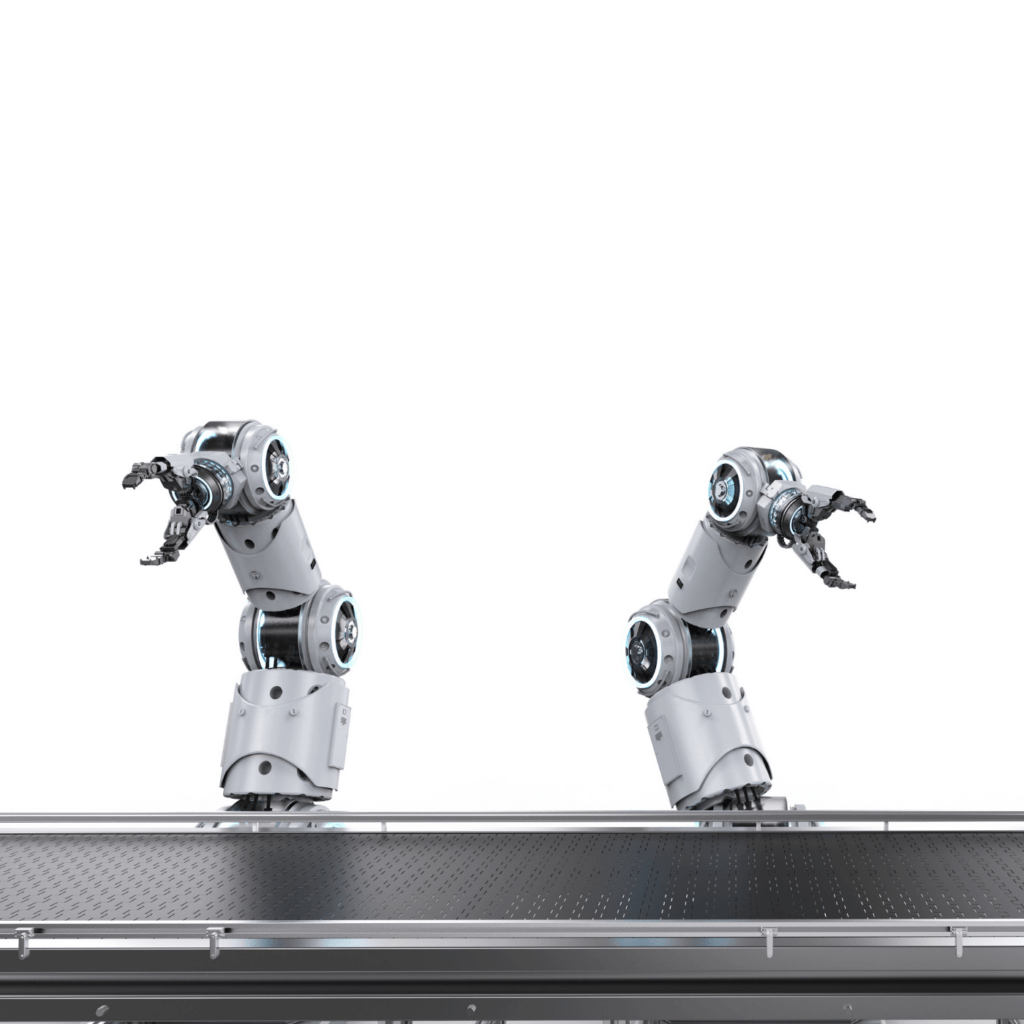
The Challenge
Differences between the virtual and physical environments due to the build-up of tolerance can seriously inhibit the effectiveness of a digital twin approach. For example, today it is typical for manual adjustments to be made to robot programs as part of a commissioning process. This manually corrects for differences in the robot position relative fixtures and the cell datum as well as correcting for the inherent inaccuracies and natural process variation with the robot. This diminishes much of the benefit gained by planning and assessing changes offline.
The Solution

Using IONA, operators can validate the position of all elements of a manufacturing system including the static robot and fixture positions and the programmed movements of each of these elements. Updates can then be made to either the digital or physical system as appropriate. This can be done at the initial commissioning stage to ensure the as built set-up matches the digital layout. The physical setup can also be monitored in real time during operation to capture any changes that occur over time.
By providing built-in connectivity with the factory network, data can be continually streamed live to the digital twin platform ensuring the digital world is continually reflecting reality.
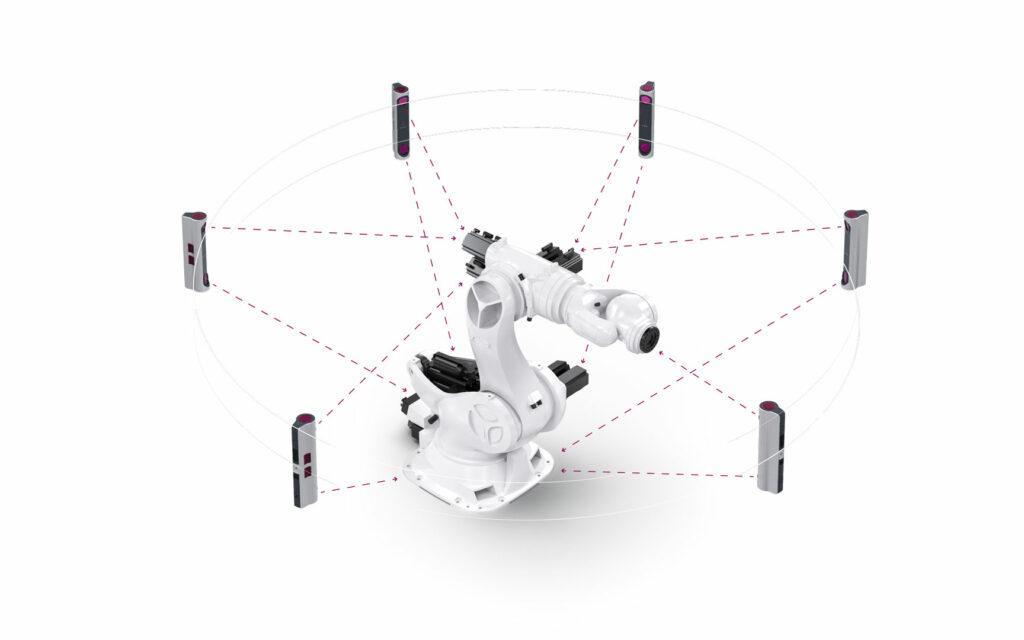
A truly flexible manufacturing system
Having a simple and effective way of validating and updating the digital twin unlocks the full potential of simulating production systems in the virtual environment. Changes can be made and assessed offline, without disrupting current production. Greater confidence can be placed in the digital simulations knowing that the digital model accurately matches the real environment and that any changes can be accurately implemented.
Making these changes without the need to manually intervene increases the system uptime and productivity and creates a truly flexible manufacturing system.
IONA Outcomes
20X
faster alignment process
Automated Robot to Part Alignment
10X
increase in process accuracy
Improves robot performance
100%
confidence through 24/7 monitoring
Continual process monitoring
Andy Silcox, Research Director, AMRC Cymru
James Allum, Senior Manufacturing Research Engineer, AMRC Cymru
Dr Stuart Morris, Engineering Director, Pentaxia
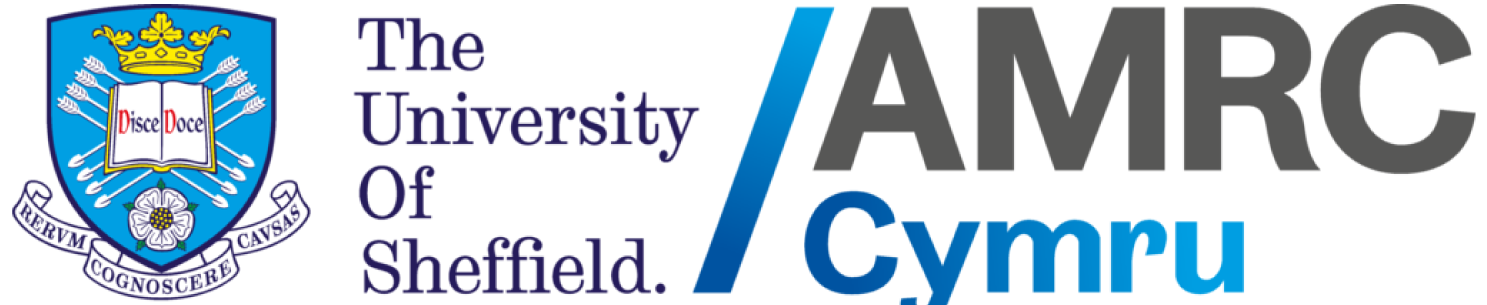
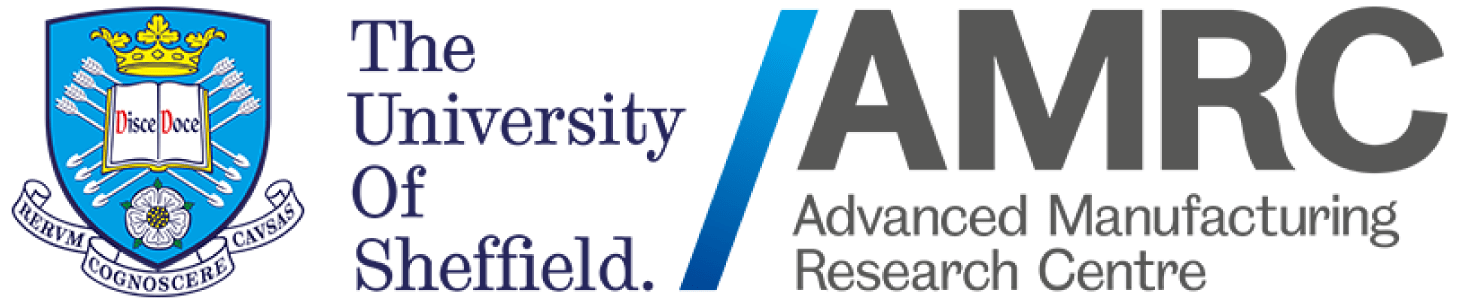
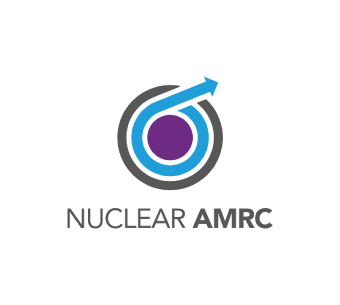
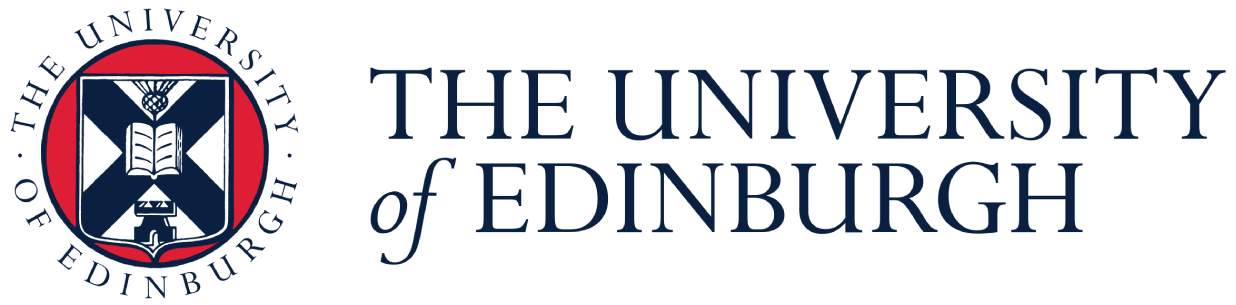
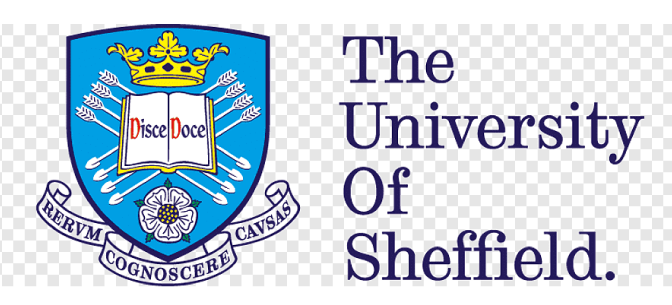
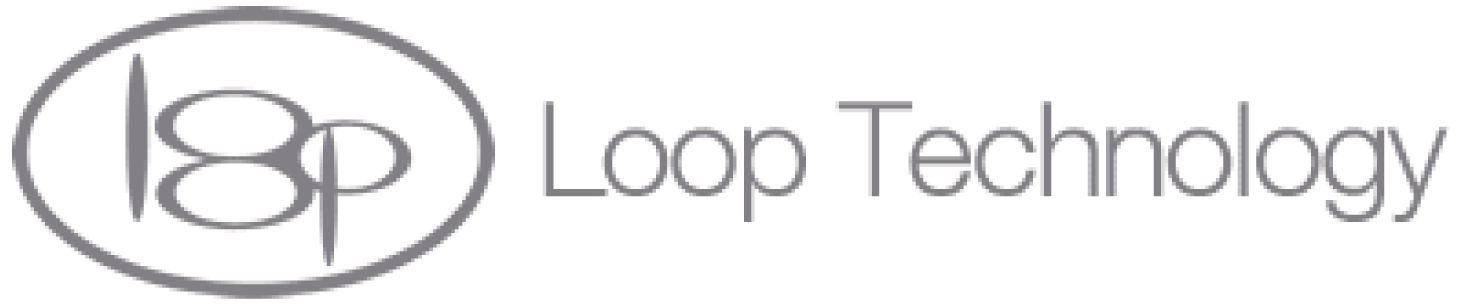
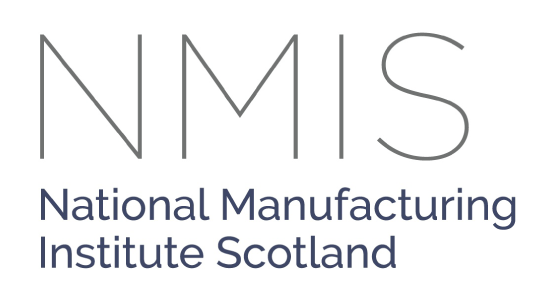
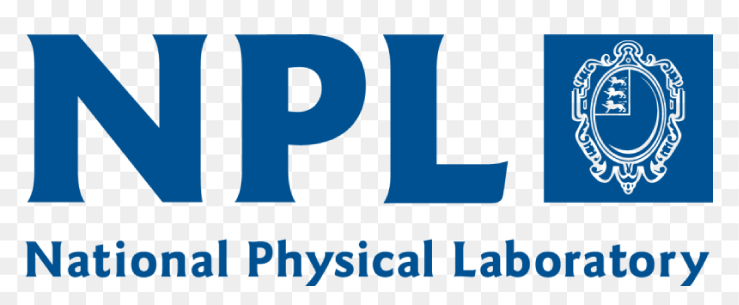
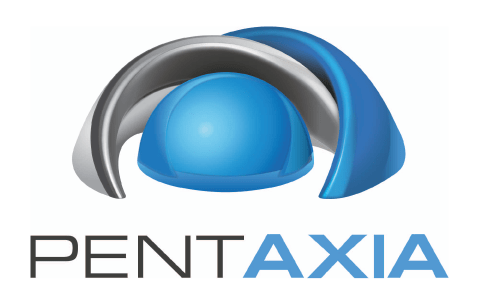
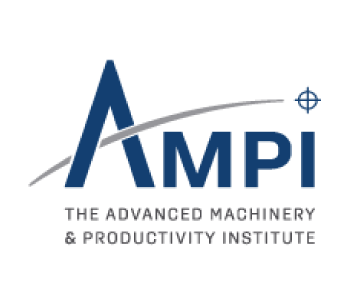
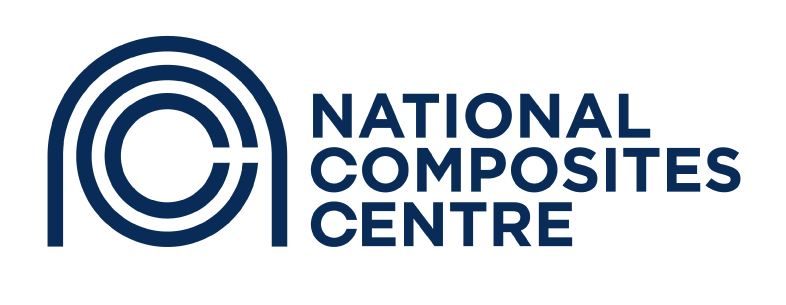
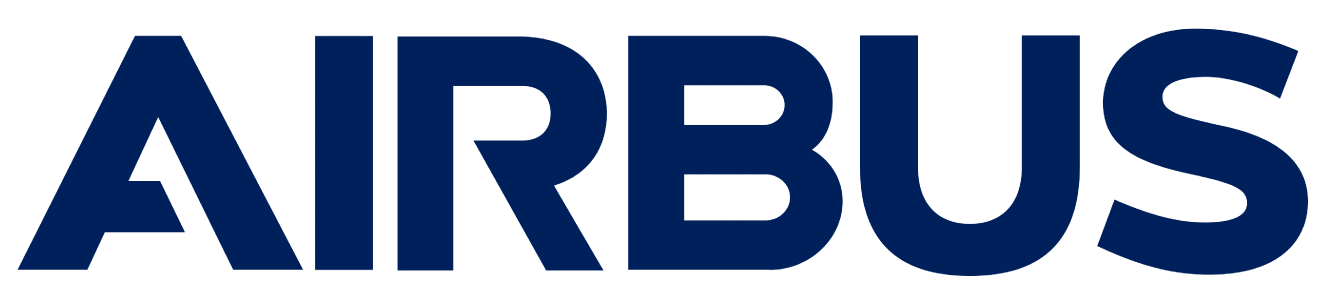
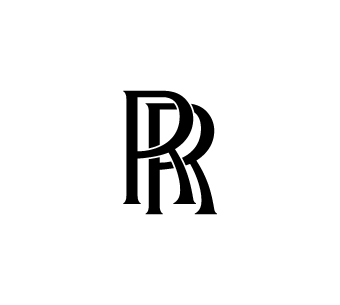
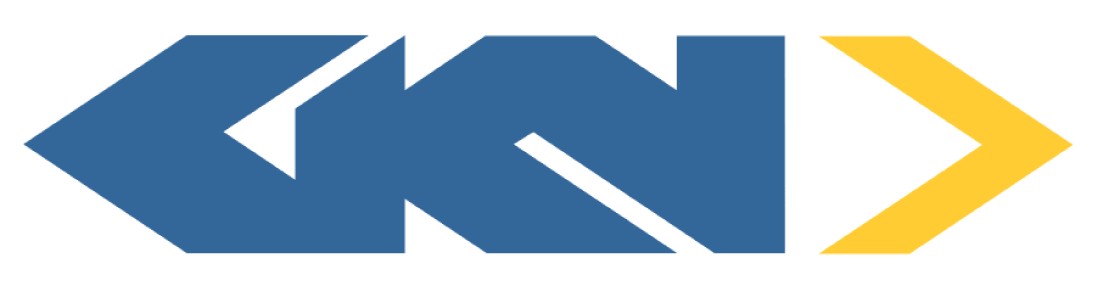
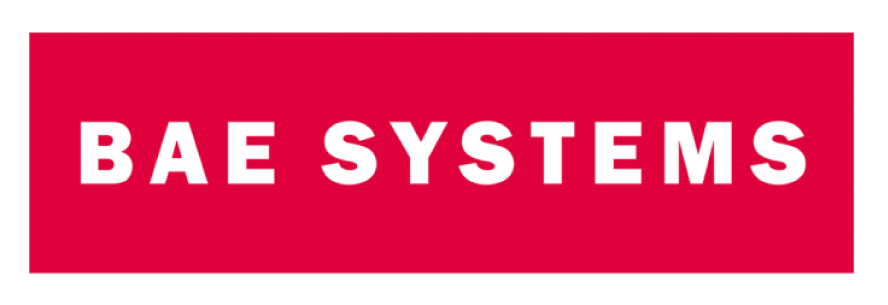
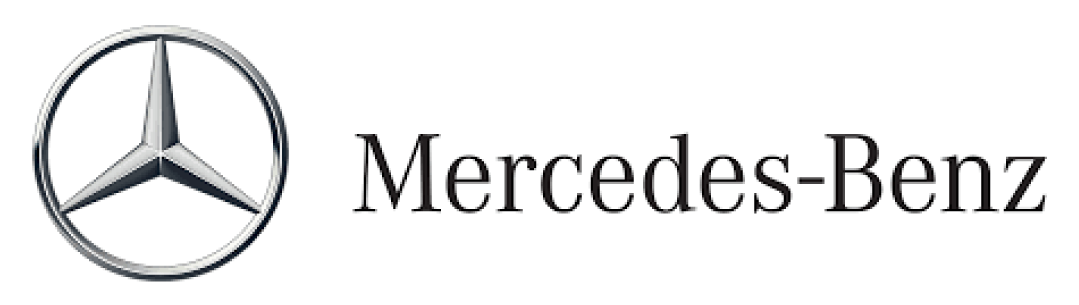
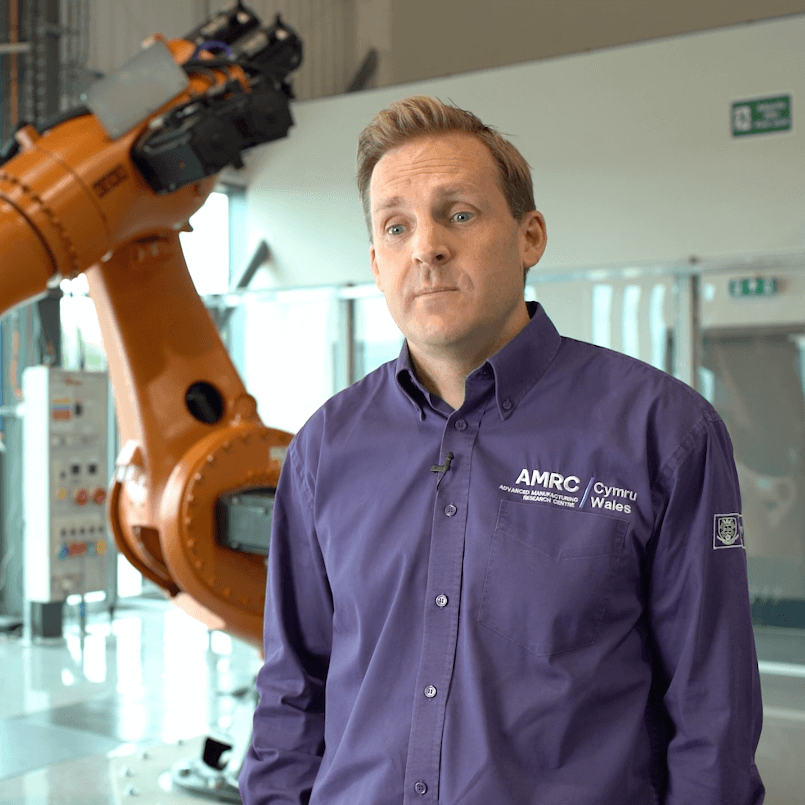
“Exciting technology!”
“IONA is a great example of some really exciting new technology that is coming to market that will revolutionise the UK Manufacturing.”
Andy Silcox, Research Director, AMRC Cymru
Revolutionising Robot Performance
Unlocking the true potential of industrial robots.