IoT Connectivity
Introducing to IoT Connectivity
The smart factory is an interconnected environment with data flowing between machines, software, operators and management to provide deeper insights and control of productivity and quality.
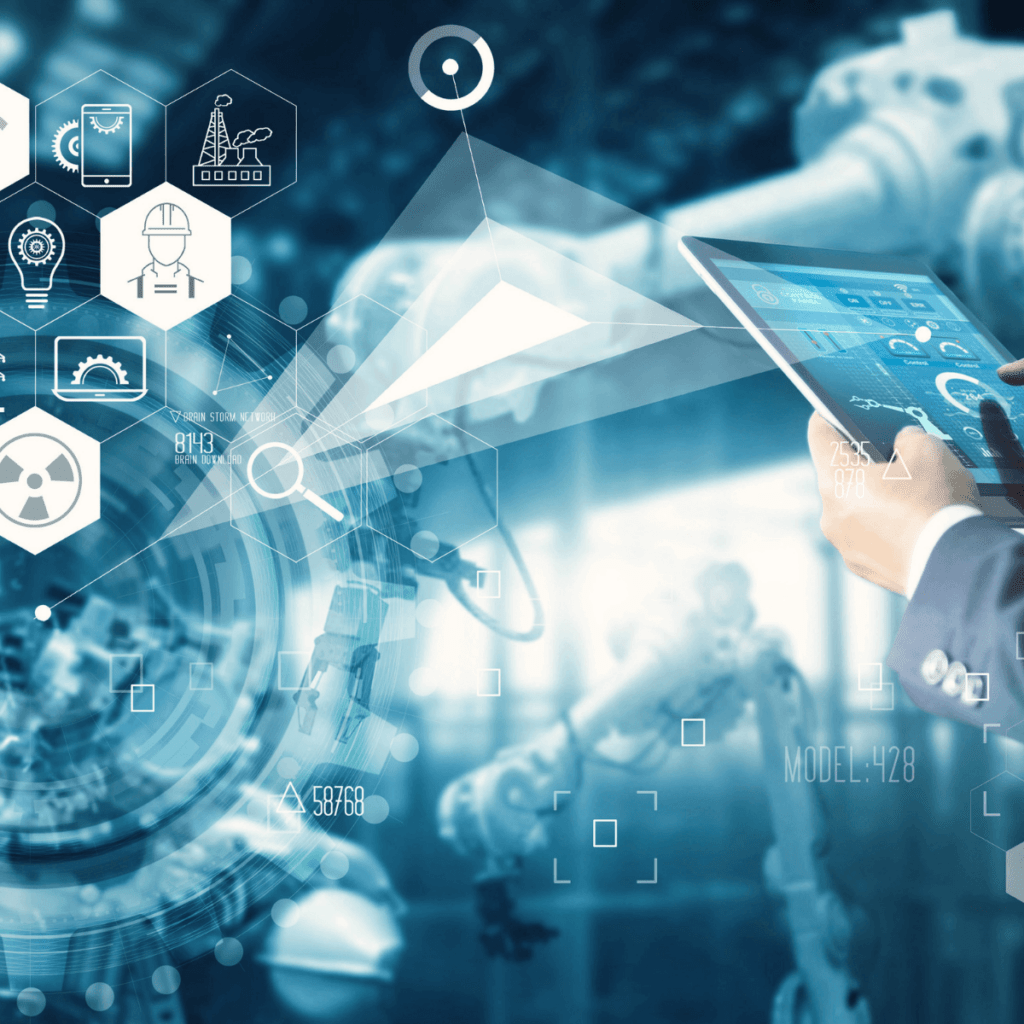
The Challenge
Machines need the ability to connect in multiple ways, at a local level within the automation cell to control the task in hand, but also at a factory level send data for further analysis and overall production planning.
Not only do the correct communication protocols need to be implemented, so too do the right type of data formats to enable different platforms to benefit from the data available.
The Solution

The IONA system provides simple turnkey integration with major robot OEMs. It communicates in native programming languages such as: KUKA KRL, ABB Rapid and Fanuc KAREL.
The software (ORA) API enables the robot to autonomously drive the processes, calling on ORAs functionality as required. This includes Verification of Robot Path, Tool and Base Calibration, Automated Fixture Alignment and Iterative TCP Correction to name a few.
ORA can operate as an autonomous ‘black-box’, fully integrated with the robot controller or cell PLC, providing data via an API as and when requested by the robot program. Alternatively, ORA can be driven by an operator via a simple user interface with a 3D environment and graphical display of the data generated. The operator can decide what to push back to the robot to update a process or what to use for further analysis.
ORA features OPC-UA and MQTT communication protocols allowing data to be seamlessly input to MES platforms at a factory level. This allows the data to be used in more advanced digital manufacturing applications such as providing live verification of a digital twin or input to details SPC analysis.
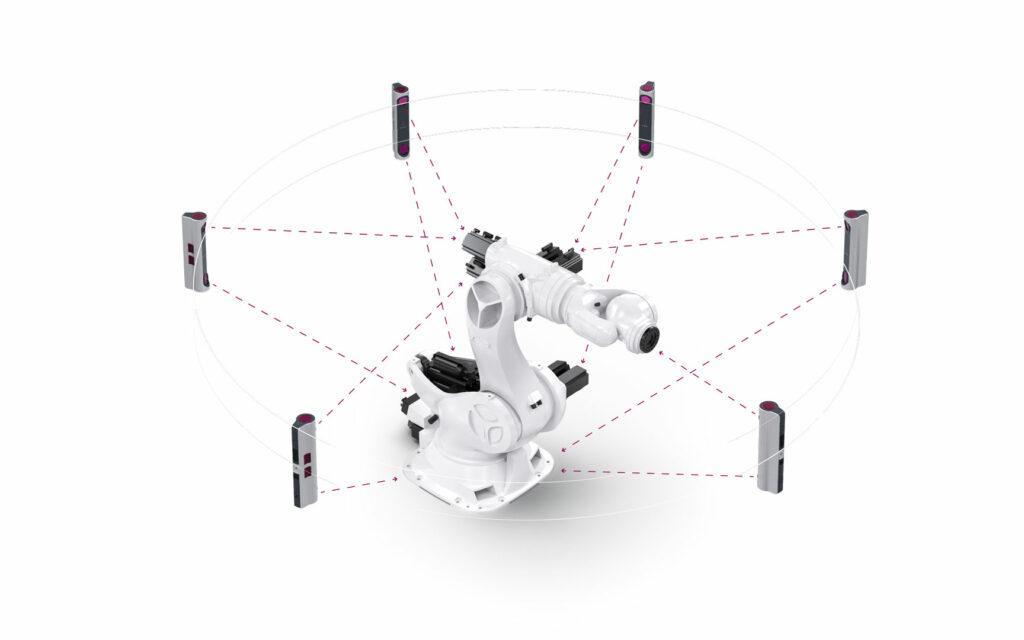
IONA System Flow
Seamlessly Integrated into the manufacturing workflow

IONA Nodes simultaneously capture live data from multiple points of interest – Robots, Fixtures, Datum features etc
The ORA software platform analyses the data from the sensor network. This can be autonomously fed back in real-time to the robot controller to correct for process variation
ORA integrates seamlessly with the broader smart factory architecture. ORA can communicate directly with the robot controller or PLC via an API as well as being able to send data directly to the MES platform at the factory level. This enables ORA to operate as a ‘black-box’ providing data autonomously on demand.
IONA Outcomes
20X
faster alignment process
Automated Robot to Part Alignment
10X
increase in process accuracy
Improves robot performance
100%
confidence through 24/7 monitoring
Continual process monitoring
Andy Silcox, Research Director, AMRC Cymru
James Allum, Senior Manufacturing Research Engineer, AMRC Cymru
Dr Stuart Morris, Engineering Director, Pentaxia
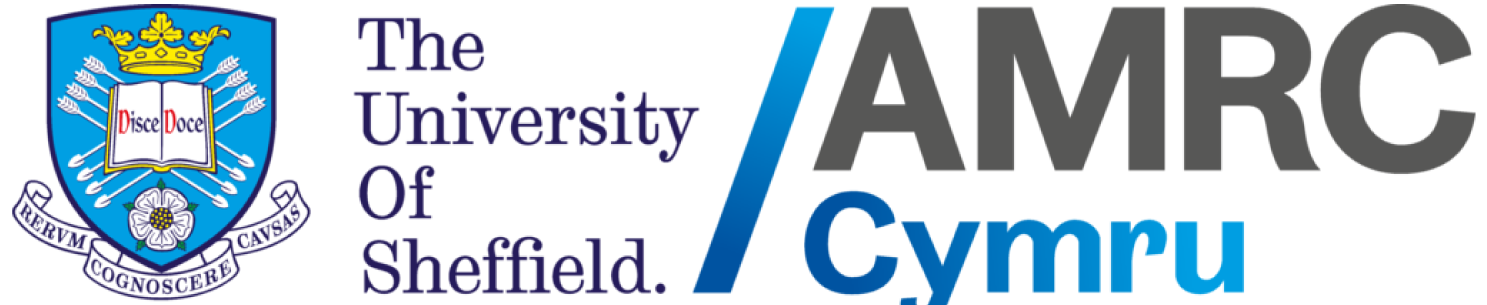
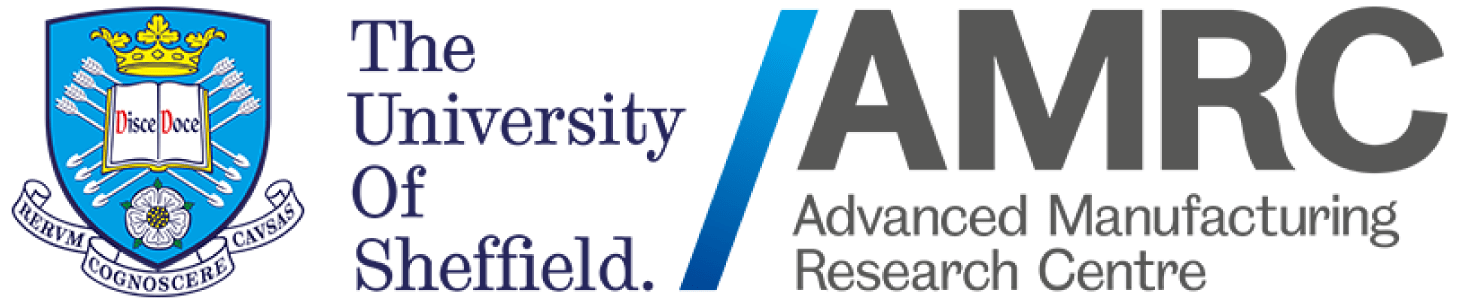
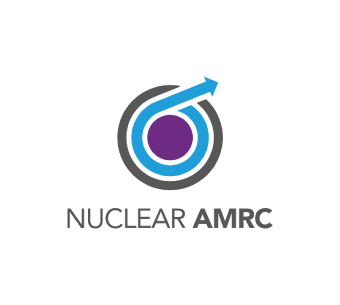
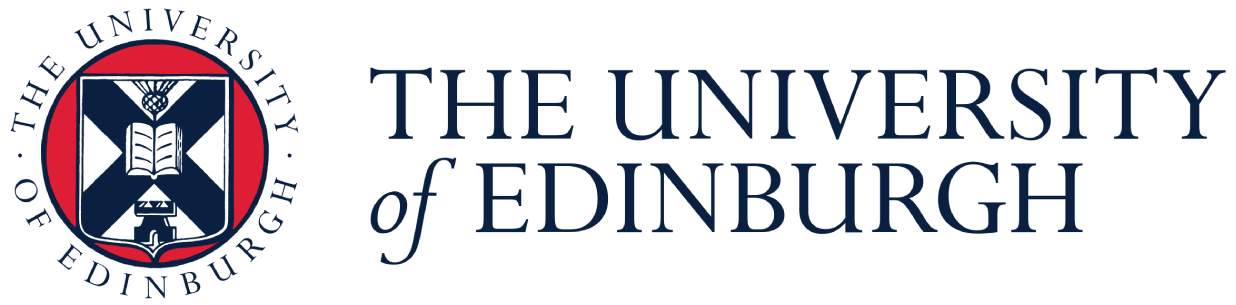
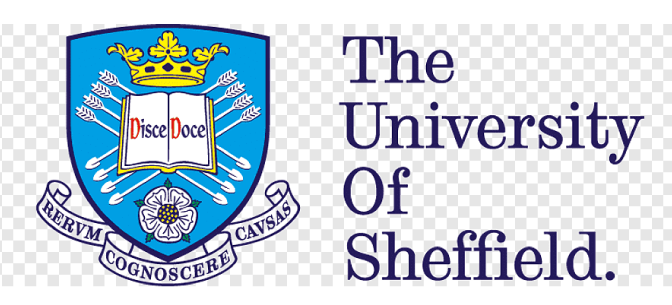
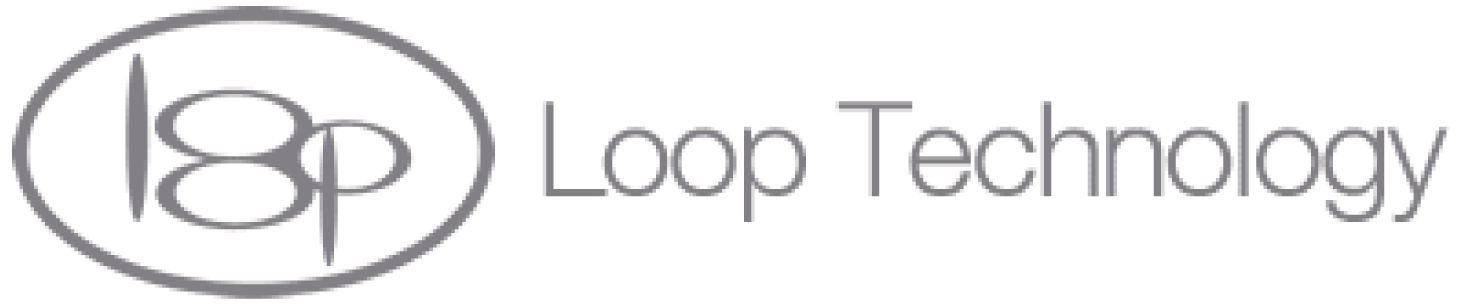
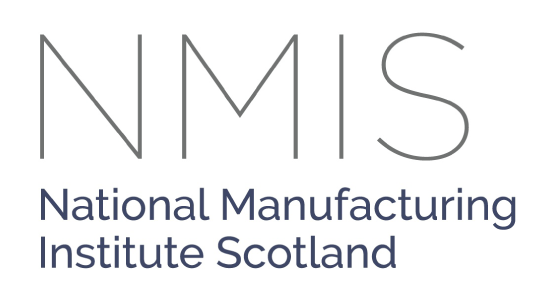
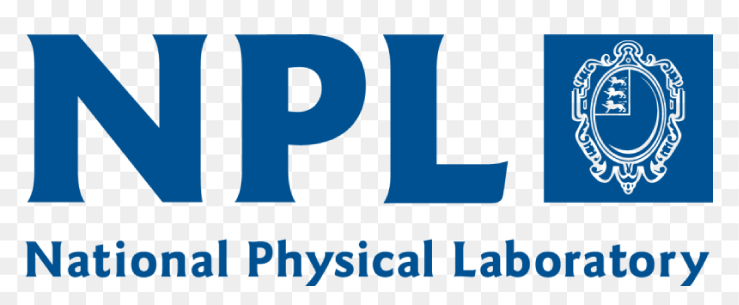
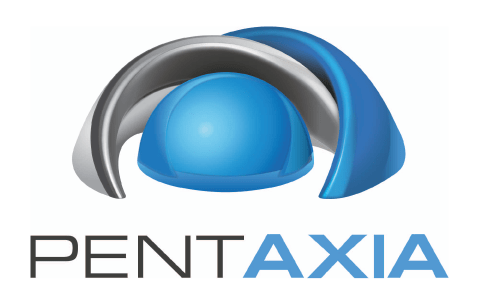
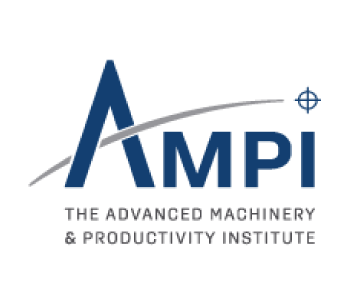
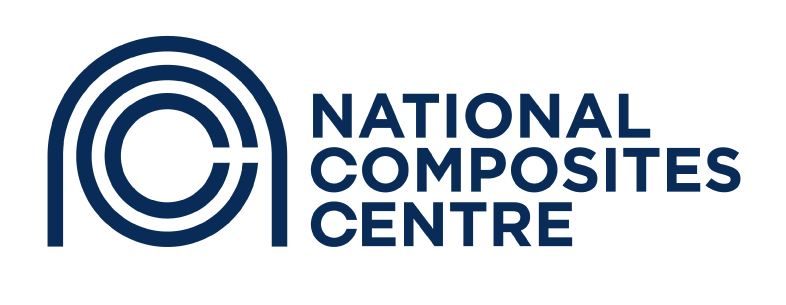
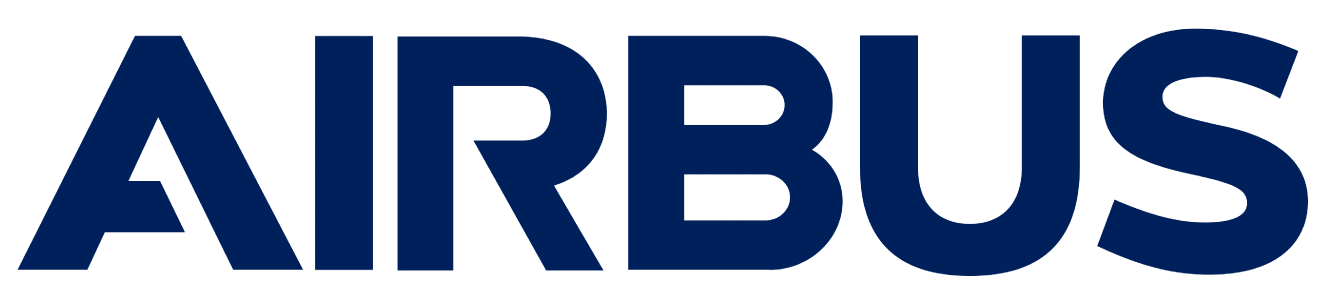
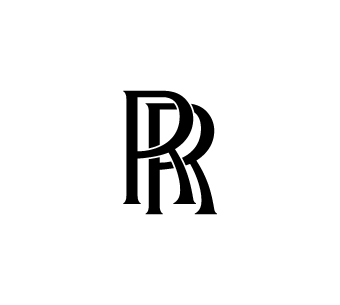
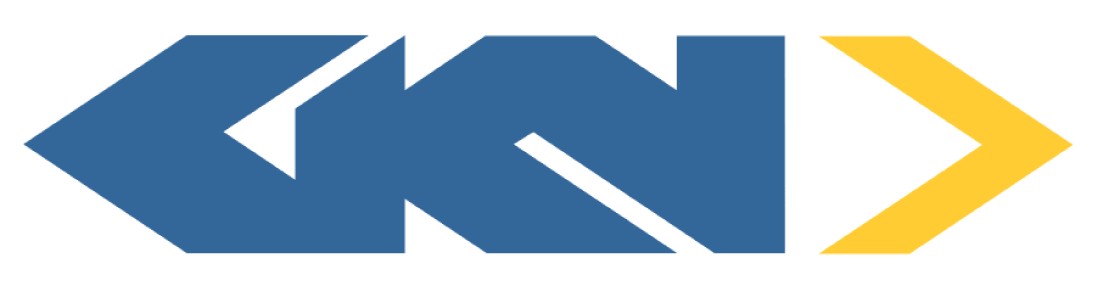
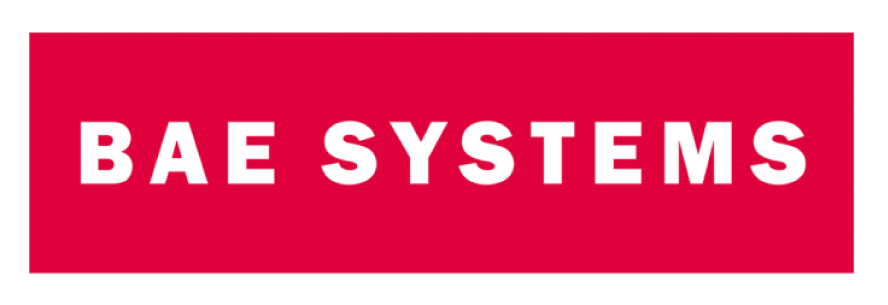
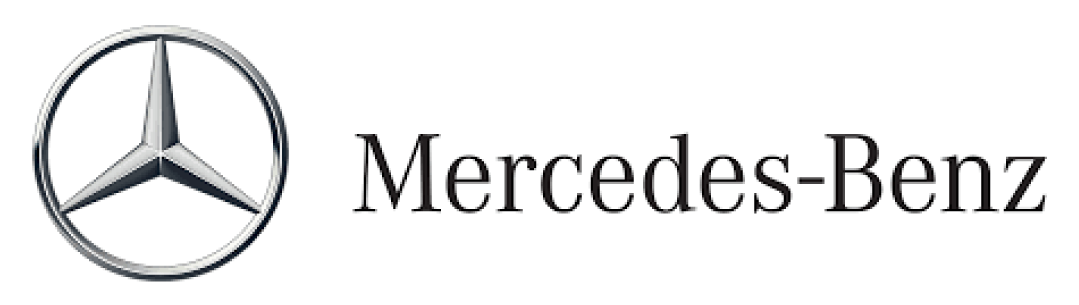
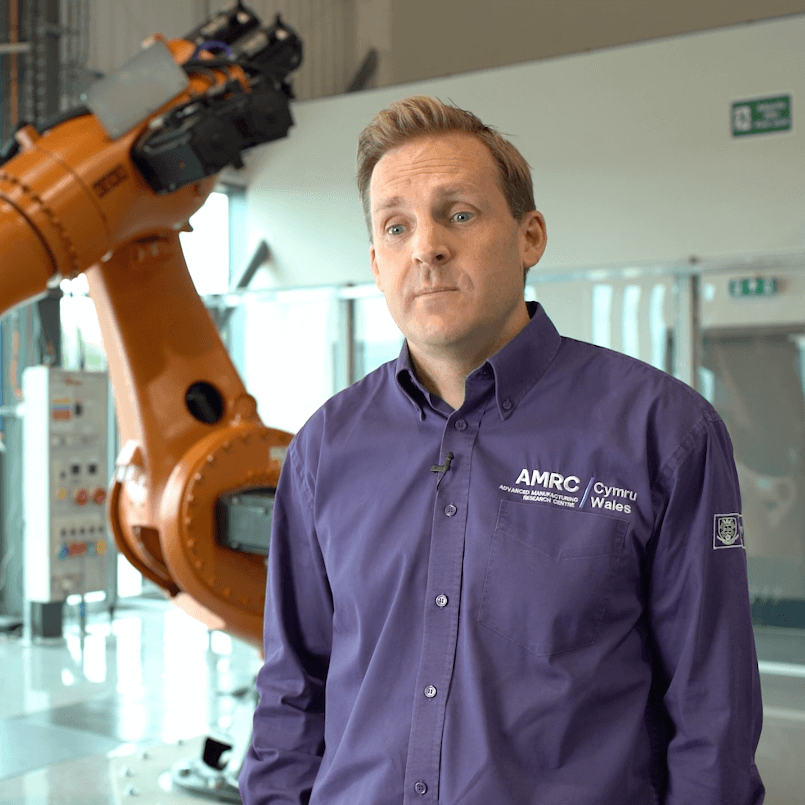
"Exciting technology"
“IONA is a great example of some really exciting new technology that is coming to market that will revolutionise the UK Manufacturing.”
Andy Silcox, Research Director, AMRC Cymru
Revolutionising Robot Performance
Unlocking the true potential of industrial robots.