Composite Manufacturing
Unlocking the true potential of industrial robots.
Introduction to Composite
Composite manufacturing has come along way since the early days of hand lay-up fibreglass. Highly sophisticated carbon laminates are now used as part of the primary airframe structure such as wing spars and fuselage bodies. Increasingly automotive manufacturers are turning to composites to lightweight vehicles in a move towards electrification. As these materials move into the mainstream, greater focus is being place on how to automate production to produce composite parts at scale.
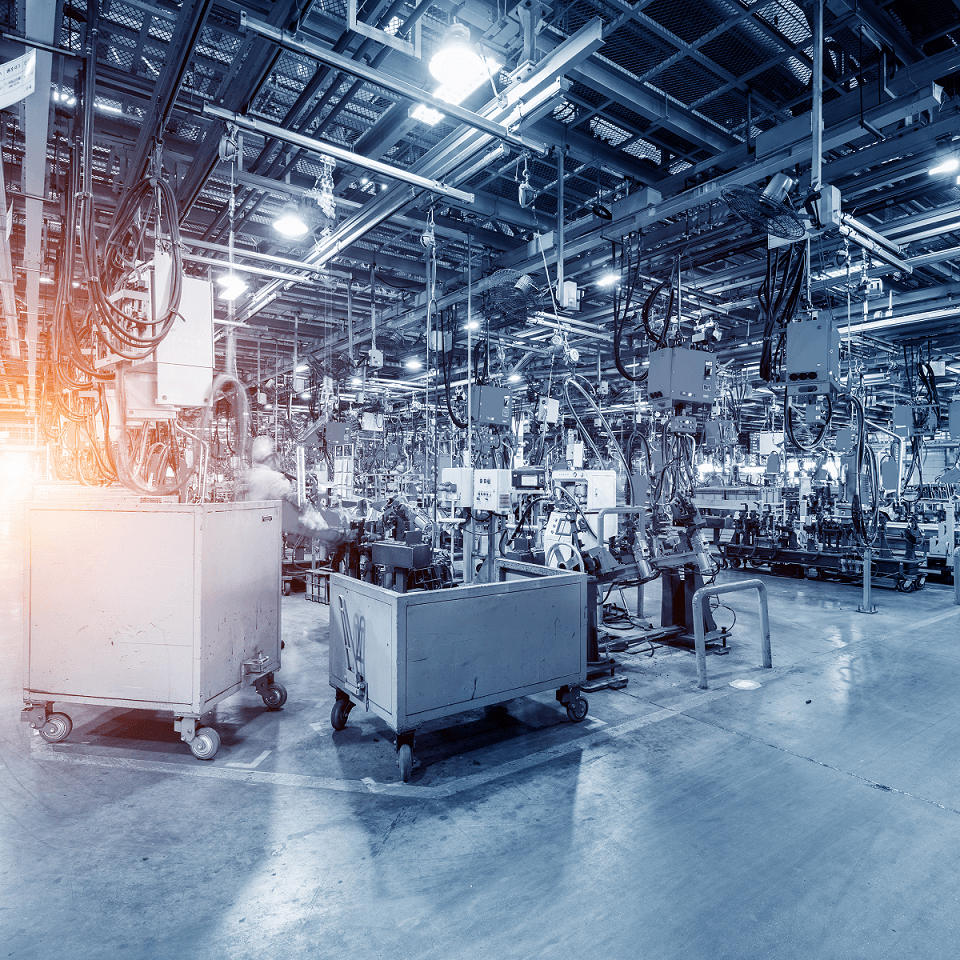
The Challenge
There are two key stages for automation in composite manufacturing – material deposition and post cure material removal including edge trimming, machining, or drilling.
Material deposition is particularly challenging in that it relies on the accuracy (rather than repeatability) of the deployment system to ensure each layer is aligned correctly.
The post-cure processes experience the same challenges as other material removal operations using a robot as a deployment mechanism – alignment to the part, process forces impacting accuracy and lack of in-process verification are all issues experienced.
The Solution

To improve material deposition, IONA can be used to calibrate the robot to take into account the dynamic loading of the deposition end effector. This calibration results in a closer match between the simulated process and the physical deposition path. The path can also be verified in-process by using IONA in monitoring mode, providing a quality check that the deposition task has been performed correctly for each layer.
The robot calibration process can also be used when trimming a cured part. This can be conducted as a one off task or periodically to ensure the robot operates within specification given the end effector load and dynamic forces. At the start of each operation, IONA can be used to correct the alignment of part to the robot. This greatly improves the accuracy and reduces the risk of producing a scrap part. The monitoring function can also be used to provide process control evidence reducing the need for 100% inspection of parts post process.
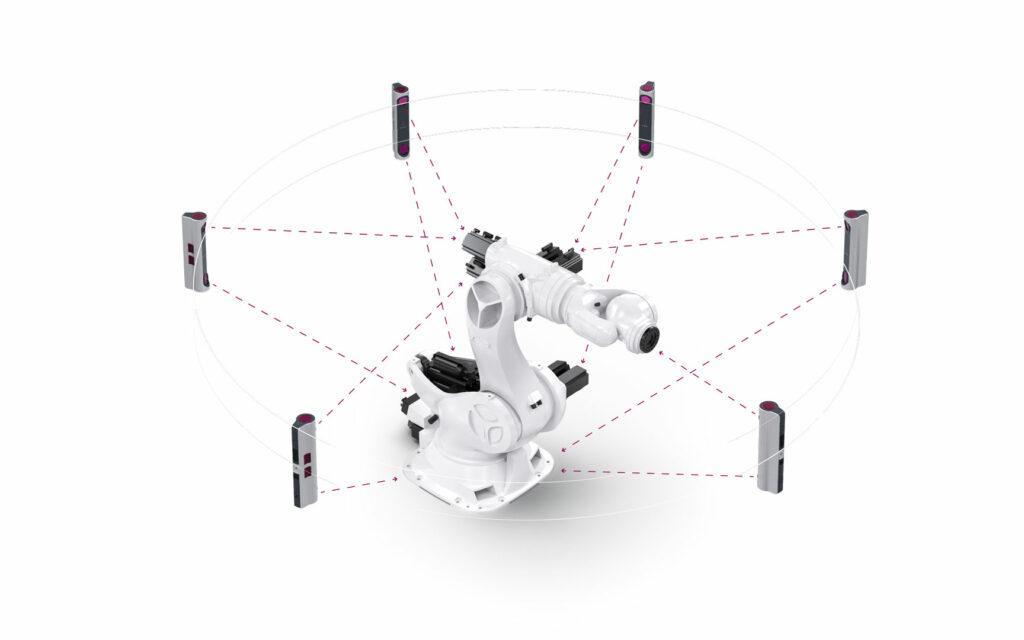
IONA Outcomes
20X
faster alignment process
Automated Robot to Part Alignment
10X
increase in process accuracy
Improves robot performance
100%
confidence through 24/7 monitoring
Continual process monitoring
Andy Silcox, Research Director, AMRC Cymru
James Allum, Senior Manufacturing Research Engineer, AMRC Cymru
Dr Stuart Morris, Engineering Director, Pentaxia
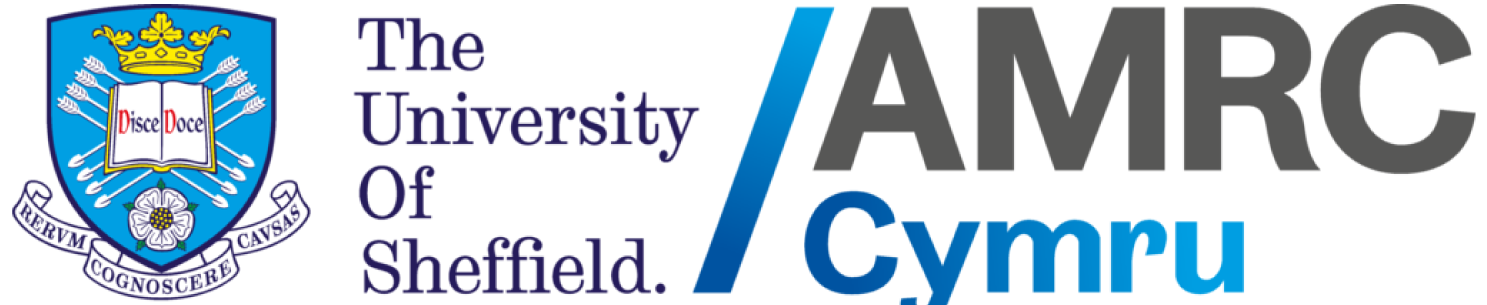
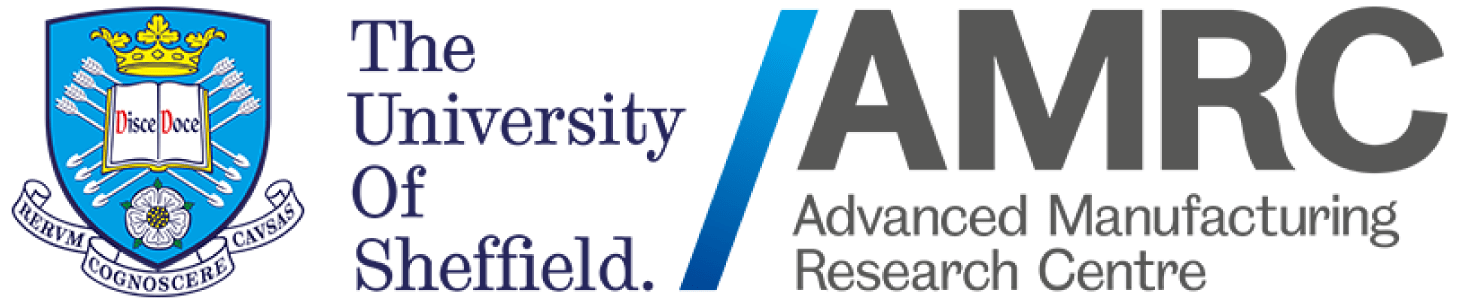
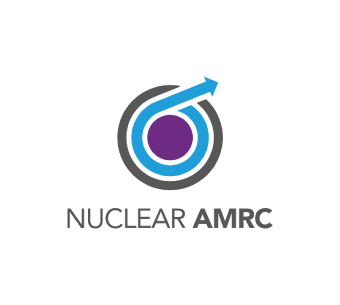
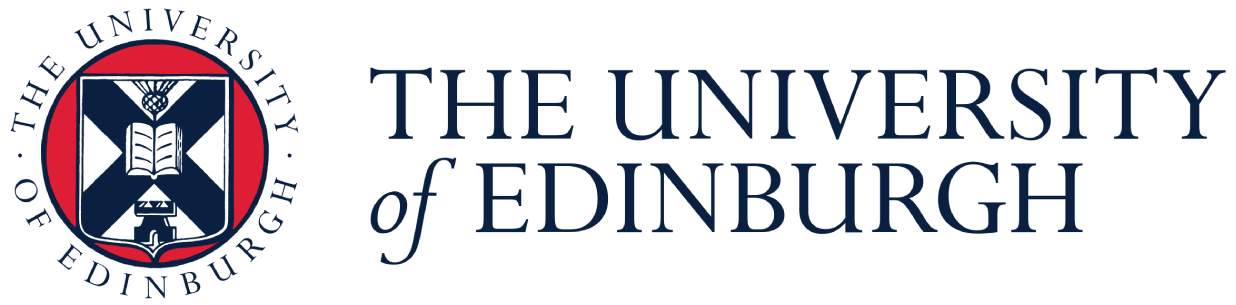
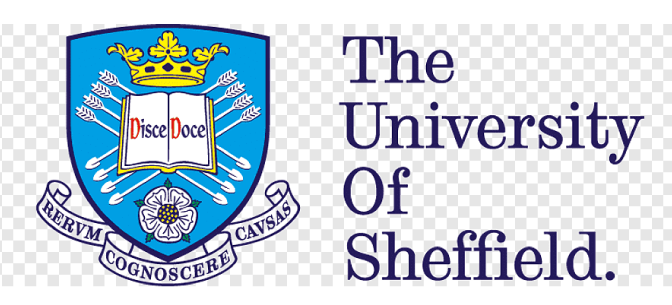
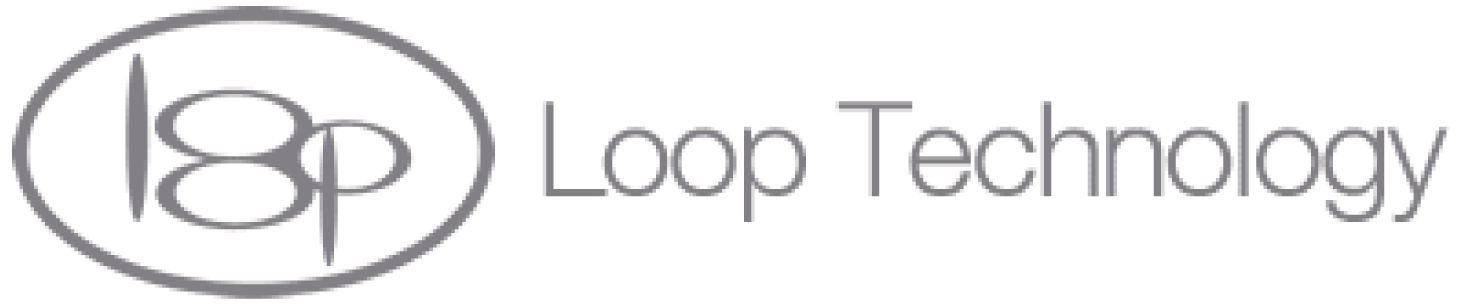
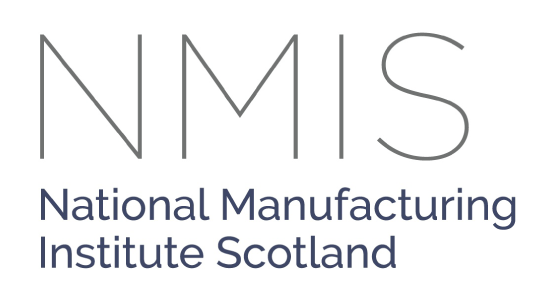
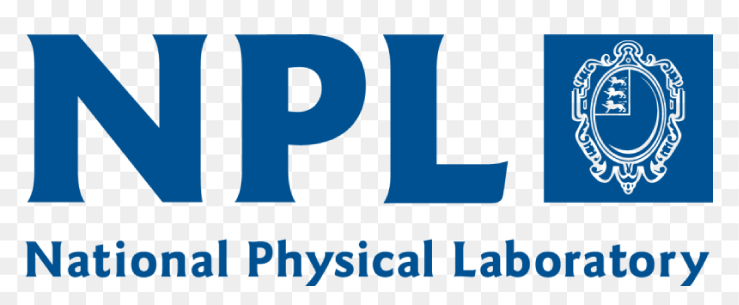
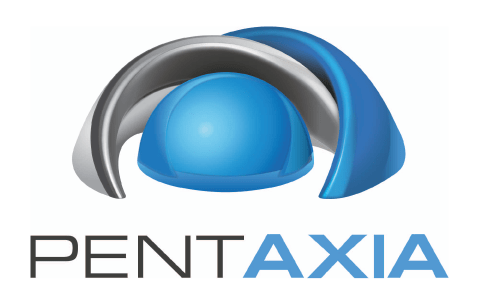
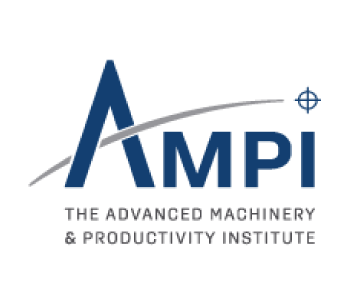
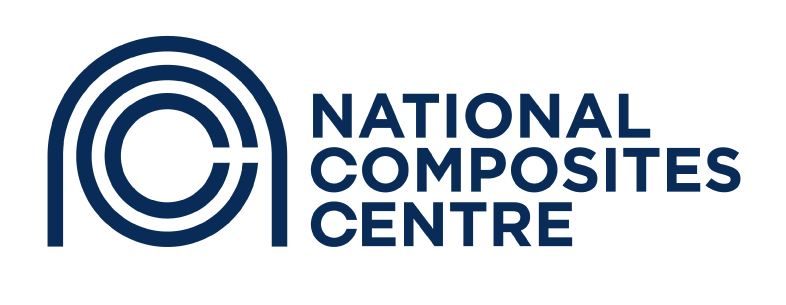
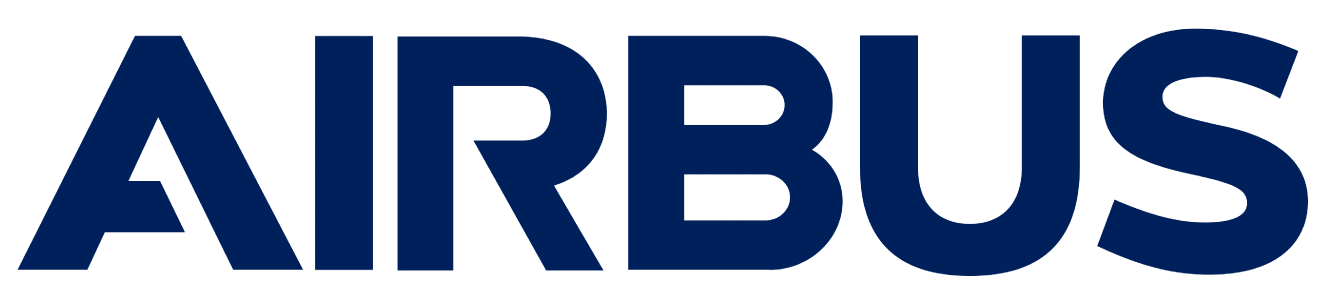
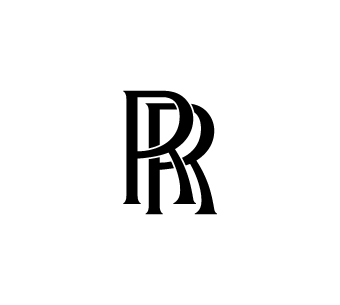
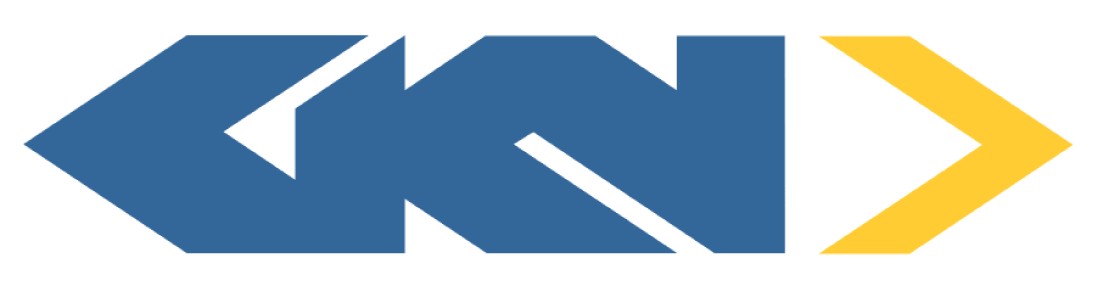
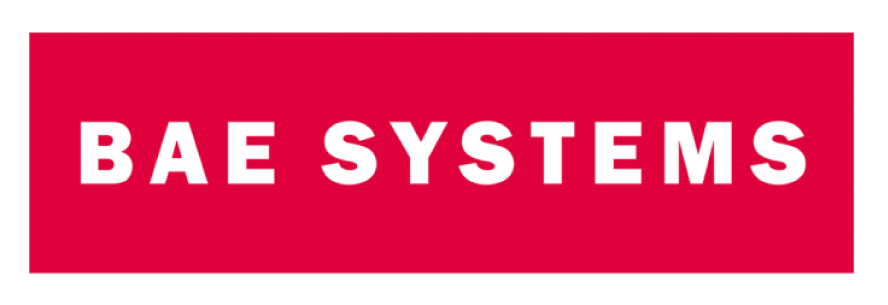
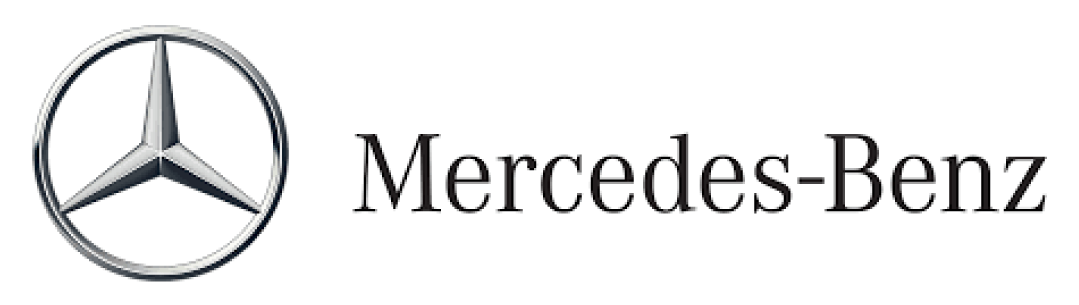
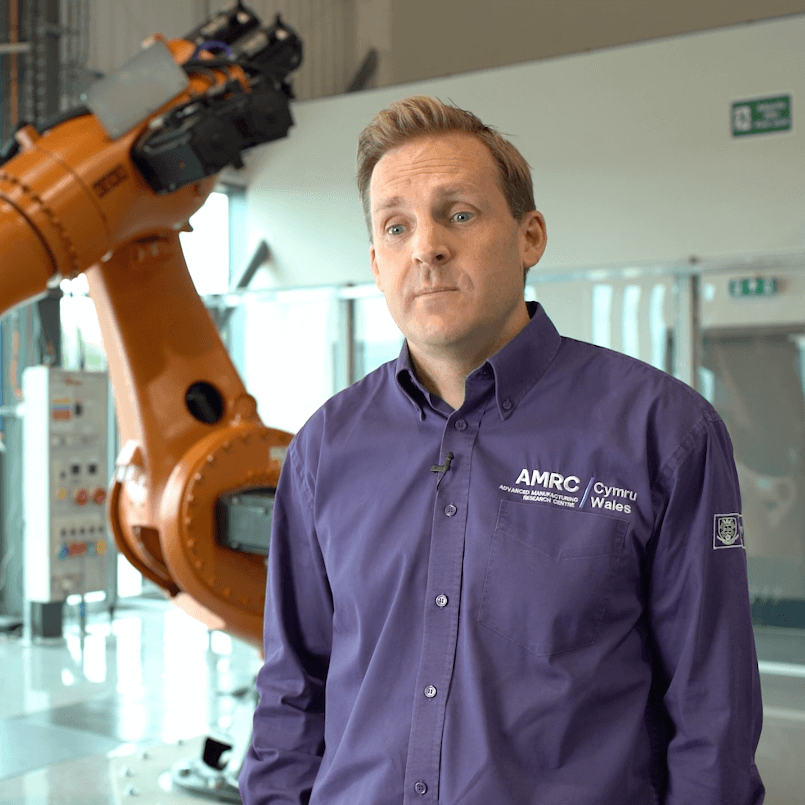
“Exciting technology!”
IONA is a great example of some really exciting new technology that is coming to market that will revolutionise the UK Manufacturing.
Andy Silcox, Research Director, AMRC Cymru
Revolutionising Robot Performance
Unlocking the true potential of industrial robots.