As is well known, the automotive sector is experiencing a period of rapid evolution, driven by consumer preferences, new technology and the ever-present need to become more environmentally sustainable. Whilst this can be clearly seen in the products emerging at the car showrooms, what is less obvious is the influence that these trends are having on how cars are produced and the automation that is making their production possible.
Clearly traditional automakers and new entrants are investing heavily in Electric Vehicle (EV) development and production. This shift required huge changes in manufacturing processes, including the integration of battery production lines, electric drivetrain assembly, and specialised EV components.
Alongside this shift to EV, there is also the drive to make vehicles more autonomous with advanced driver-assistance systems (ADAS), to improve safety and convenience.
In support of these changes, Automakers are also exploring new materials and manufacturing techniques to reduce the weight of vehicles. Light weighting is crucial for improving fuel efficiency in internal combustion engine vehicles and extending the range of electric vehicles.
So what does this mean for automation?
It has been proven time and time again that industrial robots are incredible tools for automating repetitive processes, however with this changing landscape, they alone do not have the intelligence to provide the performance and flexibility to meet the demands of manufacturing today.
Developing ‘intelligent’ automation is critical in the shift to producing electric vehicles as more flexibility in manufacturing processes is required, for reasons that will be discussed. To be more flexible, robots need context and awareness of the environment they are operating and sensor systems like IONA can provide them with this. By detecting and accurately locating parts and datum features, information can be fed back to re-align and correct a robot program and ensure an operation is performed accurately.
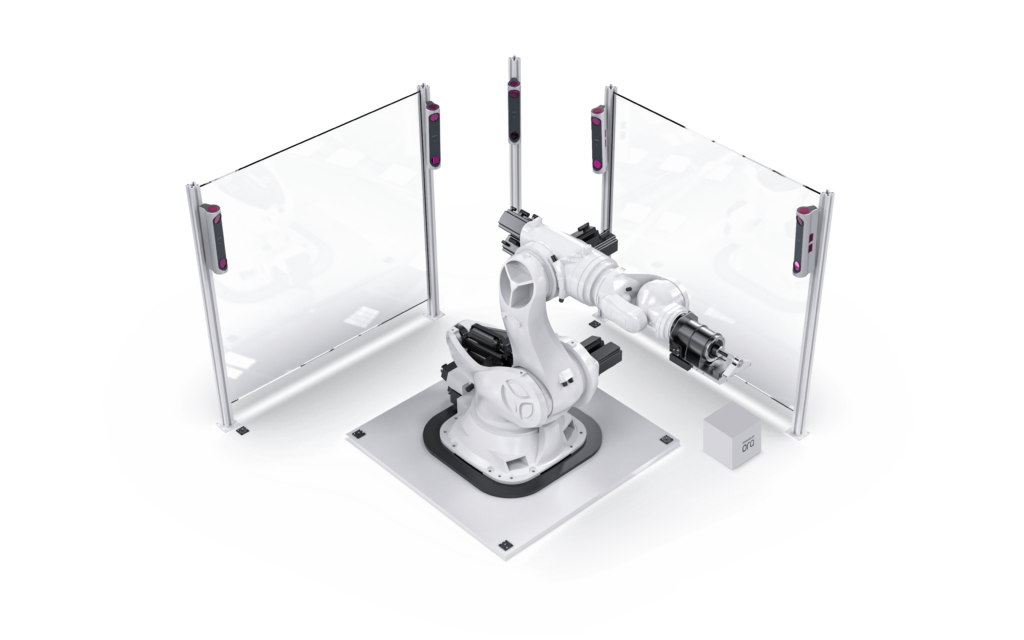
Here are 4 of the top reasons why intelligent automation is crucial in the shift to electric vehicle production:
1 – Unlocks ability to ramp up and down production levels more readily
Industry isn’t going to switch from combustion engine to battery overnight and manufacturers find themselves in a period where both EVs and combustion variants need to be produced alongside each other. As demand levels shift between model variants, manufacturers will need to ramp up and down production levels more readily. This will place a far greater emphasis on the need for modular, flexible and reconfigurable production lines.
2 – Creates more flexibility within factory footprint
The use of automated guided vehicle (AGVs) is becoming more widespread, either for logistics operations within the factory, or for moving the product between stations. Jigless assembly is another enabler of flexibility, often combined with the use of AGVs. This approach presents its own challenges for the industrial robots however. A robot needs a way to determine the accurate location and alignment of the part which is now being presented on a mobile platform. This is where sensors such as the IONA system can provide the ‘intelligence’ correcting a program based on the measured location of the robot and part datum.
3 – Speeds up takt time with more processes being automated
Sensor systems like IONA also play a role in enabling more processes to be automated. For example, manufacturing using lightweight materials such as carbon fibre and even additive manufactured parts has typically been too challenging for a robot to complete with the accuracy required. Having IONA integrated into their cell provides sensor driven guidance, robots are now able to perform tasks such as material deposition or post process trimming more accurately.
In addition to this, when a new robot program is introduced as part of a new model variant or product coming online, by giving robots increased levels of awareness through sensor technology, model changeovers are faster, initial commission processes are quicker and downtime is reduced.
4 – Improves quality and reduces waste
There are quality and productivity benefits too, with sensors monitoring and correcting robots in real time, quality issues are more likely to be caught early before they have a costly impact further downstream.
Electric vehicle production is just one of the many trends putting increased pressure on robot performance and automation. IONA is a scalable network of sensors providing metrology-grade data for industrial robots, unlocking greater flexibility and delivering intelligent, data driven automation, even during the challenging shift to electric vehicle production.
To request more information or book a demonstration, simply click the button below.