In advanced manufacturing settings, portable arms have become a familiar sight, both in inspection areas and shop-floor environments. Their versatility and usefulness have also resulted in their use spreading to a wide variety of settings beyond manufacturing, from clinical measurement in hospitals, to data-archiving of antiquities in museums.
Unrivalled Versatility
The original patent for articulated measuring arms (US3944798A) was filed in 1974 and commercial products were first launched in the early 1980s for tube-bending verification (Romer) and medical/surgical measurement (FARO). These two original applications, whilst quite separate, give a clue to the inevitable rise in popularity of articulated arms – they are used where 3-dimensional coordinate data is needed at sub-millimetre accuracy, especially where portability and flexibility are also required. Tube-bending companies typically manufacture thousands of different tube configurations over a range of sizes, all having complex 3D geometry; patients in medical settings are undeniably both 3-dimensional and unique!
With the passage of 40 years, the range of available arms has proliferated, and specialist arms have developed to improve their suitability for specific applications. Whilst non-contact laser scanning, diverse probing options, wireless connectivity, absolute encoders, and endless software enhancements have transformed the usability of portable arms, their ‘genetic code’ remains remarkably close to that of their early ancestors from the 1980s.
Advanced but Accessible Technology
All arms operate on the same principle: accurate angular encoders measure the articulations between a series of rigid shafts to enable the position of a probe to be recorded in relation to a fixed base unit. Movement of the arm’s links allows a user great flexibility to reach around parts and record data from all sides.
Many arms include a non-contact laser-line scanner in addition to a contact probe, enabling complex surface detail to be captured in the form of a point-cloud of XYZ datapoints. Using contact and non-contact probing, nearly all feature types can be measured accurately and simply.
Arms are relatively expensive, typically costing £50k or more. If they are only required intermittently, it is relatively easy to hire the equipment on a temporary basis with bespoke software and a skilled operator, if required. INSPHERE performs sub-contract service measurement work for a diverse range of clients, from f1 racing teams to artists requiring physical models to be recorded in a digital environment. An arm can be set up almost anywhere to capture true 3-dimensional datasets that respect datum structures and output full GD&T inspections quickly and efficiently. Such sub-contracting arrangements lower the barriers to entry and make coordinate metrology accessible to smaller organisations.
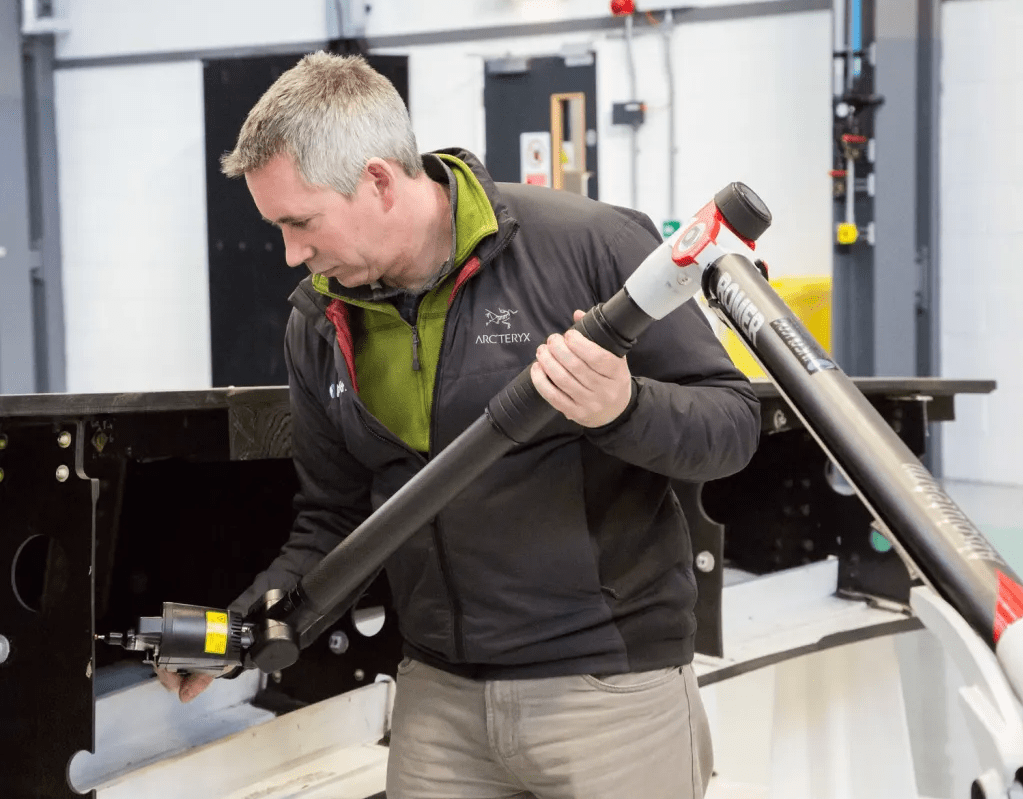
An example of INSPHERE’s recent work was to inspect a variety of configurations of air-ducts for aircraft. These had traditionally been inspected by first principles metrology but use of a portable arm allowed geometrical tolerances to be inspected far more efficiently and repeatably than by traditional methods.
Another regular inspection the company perform is to reach into the driver’s cockpit of f1 cars to establish the positions of anchor points and other key interfaces. This extremely cramped and complex space would be almost impossible to measure by any other system.
The Importance of Good Practice
One of the distinctive features of portable arms is the degree of operator influence. In comparison with other precision metrology systems, the user of an arm can markedly alter the results obtained. In this respect they are a bit like traditional ‘Vernier’ calipers – versatile, widely available, and sometimes woefully misused.
In Measurement System Analysis (MSA), ‘reproducibility’ quantifies how much a measurement system is influenced by the user. Ideally the influence of the user is close to zero. Steps to reduce such ‘nuisance’ variation can include good practice training and better documentation of work instructions to help standardise usage of the equipment.
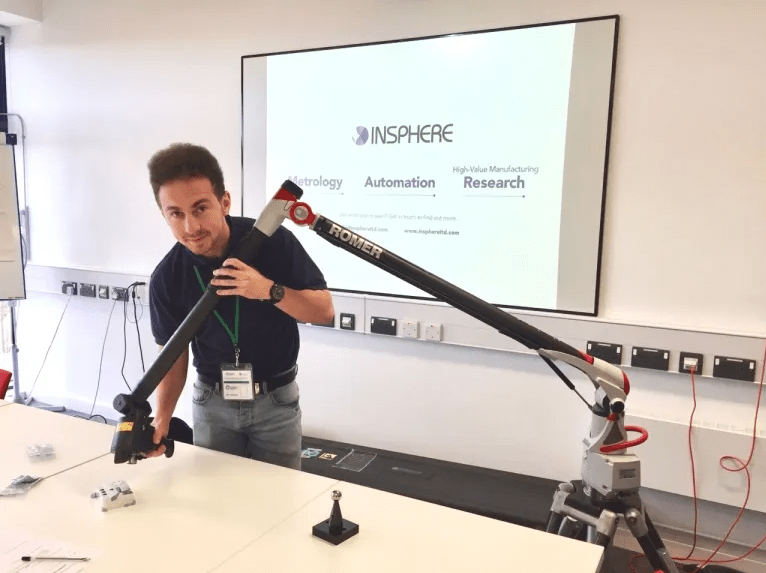
INSPHERE has had great success with its portable metrology good practice courses as they are specifically designed to empower learners to ask questions about the quality of data being collected. The training course also covers how to use tools to quantify and eliminate sources of variation and improve the documentation of calibration, verification and usage approaches. The courses are software-neutral, hardware-neutral and application-neutral. Whatever arm is being used, there are several common steps that should be taken to make sure it is gathering the best possible datasets.
INSPHERE also delivers regular NPL courses in the fundamentals of measurement. Of course, a portable arm is only useful if the operator has a clear understanding of the purpose of the measurement process, and the NPL courses are an excellent way to equip learners with the tools to understand the language of measurement and how to apply it in real situations.
For more information about sub-contract portable arm metrology services or the training courses that INSPHERE offer, email info@insphereltd.com to contact us directly.